Fundamentele organizării unui singur subiect
Linii de producție discontinue
Liniile de producție discontinue cu un singur subiect(OPPL) sunt create pentru fabricarea acelorași produse pentru o lungă perioadă de timp folosind un tip paralel-secvențial al mișcării lor prin operațiuni (locuri de muncă). Ele se caracterizează prin aceleași caracteristici generale ca și pentru alte unități structurale de producție în linie de ONPL și MNPL discutate mai devreme în acest capitol. Dar diferențele sunt și ele semnificative. Principalul lucru este imposibilitatea sincronizării operațiunilor pe linie. De aici rezultă că modelele și metodele de organizare a OPPL sunt fundamental diferite de cele considerate anterior și necesită o analiză separată.
O linie de producție discontinuă, sau cu flux directeste o linie pe care, conform condițiilor de proiectare a produsului și tehnologiei de producție, nu este posibilă menținerea continuității procesului de producție: există operațiuni care nu sunt egale ca durată şi nu multipli ai ritmului. Astfel de linii sunt de obicei folosite la prelucrarea pieselor folosind diferite tipuri de echipamente, când este dificil să se asigure redistribuirea muncii între operații pentru a le sincroniza. Liniile de producție discontinue pot funcționa doar ca linii cu ritm liber. Transportoarele cu role, rampele, toboganele etc. sunt cel mai des folosite ca vehicule.
Lipsa sincronizării duce la pauze la locul de muncă după finalizarea lucrărilor cu fiecare unitate de producție. Cantitatea de pauze este determinată de formula: tper j>0; j=1, 2. Cop. Pentru utilizarea rațională a timpului de muncă se concentrează pauzele care apar în timpul fabricării unui anumit număr de produse, muncitorul și utilajele pot fi folosite în acest moment pentru alte lucrări. . Este evident că, cu cât este mai mare numărul de produse pe care apare o astfel de concentrare, cu atât este mai ușorfolosește timpul liber. Pe de altă parte, cu atât mai mult este necesară deplasarea timpului de fabricare a produselor pentru concentrarea acestuia, ceea ce înseamnă perturbarea continuității mișcării fiecărui produs prin operațiuni și creșterea îmbătrânirii acestuia. Directorul de producție se confruntă în primul rând cu rezolvarea acestei situații contradictorii atunci când organizează activitatea OPPL.
Să notăm cu n numărul de produse pe care are loc concentrarea întreruperilor și lucrul operațiilor de linie. Înmulțiți ambele părți ale ecuației de mai sus cu această valoare:
Să desemnăm timpul total al pauzei concentrate tper j nob/qj = Tper j , timpul total al lucrării concentrate tjnob/qj = Tj, ritmul părții din spate sau perioada de întoarcere a liniei rlnob = Rob. Apoi
Perioada de rotație a liniei —intervalul de timp după care linia își repetă complet starea, iar la fiecare dintre operațiunile sale se produce același număr de produse nturn, numitturnaround lot.
Produsele aflate între operațiuni formeazărezerva de cifră de afaceri interoperațională.Valoarea acesteia se modifică în timp. Graficul schimbării, construit pe un interval egal cu perioada de rotație a liniilor, se numeștediagramaa restanțelor. Se construiesc parcele pentru fiecare pereche de operații pe linii adiacente. Restul apare din cauza diferențelor de performanță și/sau din cauza unei schimbări în începerea lucrărilor la operațiunile adiacente. Valoarea acestuia este proporțională cu valorile acestor doi parametri, precum și cu dimensiunea lotului circulant. Un interes deosebit pentru manager este calculul maximului, al mediei și al reportului pentru fiecare pereche de operațiuni adiacente și pentru linia în ansamblu. Valoarea restanțelor maxime determină nevoia de spații sau spații de depozitare direct la locurile de muncă alocate pentru stocarea restanțelor interoperaționale. Valoarerestul rulant este utilizat pentru controlul operațional al progresului producției. Restul mediu în termeni de valoare este cea mai importantă componentă a volumului de lucru în derulare pe linie.
Modele și metode de calcul a restanțelor
Luați în considerare regulile pentru construirea diagramelor de backlog:
1) graficul este o funcție continuă liniară pe bucăți;
2) valoarea restanțelor variază de la zero la o anumită valoare maximă; acesta esteramatul maximMax plită ;
3) rezerva de cifra de afaceri la inceputul perioadei de cifra de afaceri este egala cu rezerva de la sfarsitul perioadei; acesta esterama de tranzițieNob max.Trasarea și calcularea parametrilor de întârziere pentru o pereche arbitrară de operații adiacente j și j+1 includ următorii pași.
1. Perioada de rotație a liniei este împărțită în intervale în care stările de funcționare sunt neschimbate.
2. Pentru fiecare interval, se rezolvă problema naturii modificării în restanță:
a) crește dacă operațiunea de completare a restanțelor este mai productivă decât cea de prelevare din restante, ținând cont de numărul de locuri de muncă care lucrează în acest interval;
b) scade dacă operaţiunea de reaprovizionare este mai puţin productivă;
c) este neschimbat dacă ambele operații din pereche sunt la fel de productive (inclusiv ambele nu sunt efectuate).
3. Funcțiile liniare pe toate intervalele sunt conectate într-o singură diagramă pe baza regulilor de construire a diagramelor prezentate mai devreme.
4. Pentru fiecare interval, modificarea valorii restanțelor se calculează conform formulei:
unde Tf -durataf-al-lea interval;
qjf ,qj+1 feste numărul de lucrări pe operațiile j-a și (j+1)-a efectuate pef- al-lea interval.
5. Pornind de la punctul zero, metoda lanțului calculează restanța în toate cele criticereprezentați punctele (la limitele intervalului) folosind valorile obținute anterior DHfj, j+1; în acest caz, o parte din calcule se poate dovedi a fi redundantă dacă valorile necesare au fost deja găsite.
6. Valoarea restanțelor medii Nob cp se calculează ca înălțime a unui dreptunghi, egală ca mărime cu cifra formată de diagrama de restanțe.
Să luăm în considerare o pereche de operațiuni OPPL conexe. Fie Rb = 4h; nr6 = 80 buc; t1 = 1,1 min; t2 = 1,8 min. Este necesar pentru a construi diagrame de backlog și a calcula
Hob m ah , Hob lane și Hob avg la diferite schimburi de la începutul operațiunilor unul față de celălalt (Tsdv).
Să începem calculul prin determinarea ritmului liniei, a numărului de locuri de muncă în operațiuni și a timpului în care lucrează în perioada de rulaj:
1. Fie Tsdv=0 și ambele operațiuni încep la începutul perioadei de rotație a liniei. Apoi, pe perioada cifrei de afaceri, evidențiază trei intervale (Fig. 12.11). La prima se efectuează ambele operații, iar prima este mai productivă (t1 max ia cea mai mică valoare dacă timpul de execuție al operației mai mici din pereche se încadrează complet în timpul de execuție al celei mai mari, indiferent de schimbarea începutului lor și ordinea în care se succed.
2. Când schimbarea crește cu încălcarea condiției specificate, valoarea lui Hobj, j+1 max crește și atinge valoarea sa maximă la schimbarea maximă.
3. Dacă, la o anumită valoare a schimbului, operațiile încetează să se suprapună (nu au un timp de funcționare comun), valoarea lui Hobj, j+1 max atinge maximul, egal cu nb,și nu crește odată cu o creștere suplimentară a schimbului.
Aceste caracteristici trebuie să fie luate în considerare de către managerul de producție,definind regulile de funcționare a liniei,și anume, stabilind ora de începere pentru toate operațiunile. Criteriul în acest caz este reducerea la minimum a valorilor rezervelor de cifra de afaceri pe toate perechile de operațiuni adiacente.Cu toate acestea, acesta nu este singurul criteriu. Un alt criteriu care îl contrazice este optimizarea utilizării forței de muncă pe linie. Contradictoriu pentru că, după cum se vede din exemplul luat în considerare, un lucrător poate fi folosit în două operațiuni numai dacă operațiunile nu se suprapun în timp și, prin urmare, rezerva dintre ele este maximă. Utilizarea rațională a forței de muncă aici poate fi realizată prin organizarea de întreținere consistentă a mai multor mașini. Sarcina de a determina programul de funcționare a liniei devine mai dificilă atunci când se folosesc mai multe locuri de muncă pentru a efectua operația. Pentru astfel de operațiuni, sunt posibile două variante tipice ale programului de lucru:
1) cu încărcare uniformă a tuturor locurilor de muncă;
2) cu o încărcătură completă a tuturor locurilor de muncă, cu excepția ultimului. Prima opțiune este oportună dacă se poate organiza întreținerea paralelă cu mai multe mașini la operațiune. În caz contrar, a doua opțiune este cea mai bună, deoarece aici toate locurile de muncă, cu excepția ultimei, sunt încărcate optim - complet, iar la ultima este posibil să se folosească un lucrător parțial liber pentru alte operațiuni. În cazuri specifice, pot exista și alte opțiuni organizatorice pentru activitatea OPPL.
Fie Rb = 44; frunte = 80 buc; t1 = 4,2 min; t2 = 1,7 min. Apoi rl=3 min; q1 = (4,2/3) + 1 = 2 unități; q2= (1,7/3) + 1 = 1 unitate; T1=4,2 x 80/2 = 168 min; T2 = 1,7x80 = 136 min.
1. Dacă la prima operațiune este posibilă organizarea de întreținere paralelă pe mai multe mașini a două lucrări de către un muncitor (Fig. 12.13,a),atunci
Nob1,2 cp \u003d [(15,2 x 168) / 2 + 15,2 x (240 -168)] / 240 \u003d 9,9 \u003d 10 buc.
2. Dacă este imposibil să organizați întreținerea paralelă a mai multor mașini la prima operațiune, atunci mai multo altă versiune a regulamentului se poate dovedi a fi rațională (Fig. 12.13,b).
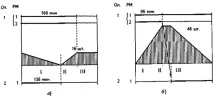
Orez. 12.13. Programe de lucru pentru două operațiuni adiacente OPPL și diagrame
restanță între ele: a - încărcarea uniformă a locurilor de muncă
(RM) la prima operație (Op.), unde o paralelă
serviciu cu mai multe stații;b -sarcina completă a primului lucrător
locuri și al doilea parțial la prima operație; Pot fi
serviciu secvenţial organizat cu mai multe staţii
În acest caz, calculul anterior al valorii lui T1 se dovedește a fi incorect. În prima operațiune, lucrătorii sunt încărcați diferit:
T11=240 min (încărcare completă);
T12 \u003d 4,2 x 80 - 240 \u003d 96 de minute (încărcare parțială).
Să stabilim programul astfel încât segmentele T12 și T2 să nu se suprapună și să fie posibilă organizarea secvenţială a serviciului multi-staţie la al doilea loc de muncă la prima și a doua operațiune (săgeata din Fig. 12.13,barată trecerea lucrătorului). Hai sa facem calculele:
Nob1.2 max \u003d [Nob1.2 III] \u003d [136 x (1 / 4,2 - 1 / 1,7)] \u003d 47,6 \u003d 48 buc;
Cu ajutorul metodelor discutate mai sus, managerul de operațiuni modelează diverse opțiuni de organizare a activității OPPL și o alege pe cea mai bună dintre acestea în opinia sa. Pentru această opțiune, rezultatele modelării analitice și ale modelelor grafice ale modificărilor de backlog, adică diagramele de backlog, precum și programele pentru efectuarea operațiunilor și a muncii lucrătorilor, sunt rezumate într-un singur document, care este transferat în producție sub numele „Standard”. plan de lucru pentru OPPL”. Are forma prezentată în tabel. 12.2 (aici nu există un grafic cu diagrame de backlog). Planul standard definește programul cel mai potrivit pentru funcționarea unei linii de producție discontinue: perioada de cifra de afaceri T0 (sau, respectiv, nb), timpul de funcționarea fiecărui loc de muncă pentru toate operațiunile, mărimea stocurilor de lucru, numărul de lucrători angajați pe linie, ținând cont de întreținerea multi-mașini, succesiunea și frecvența trecerii lucrătorilor de la exploatare la exploatare, factorii de încărcare ai locurilor de muncă.