Exemple de soluții la probleme din știința materialelor
Călirea oțelului hipoeutectoid constă în încălzirea oțelului la o temperatură peste cea critică (Ac3), în menținerea și răcirea ulterioară cu o viteză care depășește cea critică.
Temperatura punctului Ac3 pentru oțelul 40 este de 790°C.
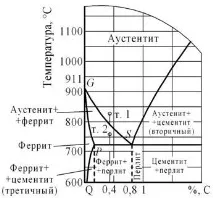
Figura 5 - Fragment din diagrama fier-carbon
Oțelurile hipoeutectoide pentru călire trebuie încălzite la o temperatură de 30-50 ° C peste Ac3.
Astfel, o parte întărită de la o temperatură de 830°C va avea proprietăți de performanță mai ridicate.
Unul dintre procesele tehnologice ale tratamentului de călire este tratamentul termomecanic (TMT).
Prelucrarea termomecanică se referă la metodele combinate de modificare a structurii și proprietăților materialelor.
Prelucrarea termomecanică combină deformarea plastică și tratamentul termic (călirea oțelului predeformat în stare austenitică).
Avantajul tratamentului termomecanic este că, cu o creștere semnificativă a rezistenței, caracteristicile de ductilitate scad ușor, iar rezistența la impact este de 1,5-2 ori mai mare în comparație cu rezistența la impact pentru același oțel după călire cu călire scăzută.
În funcție de temperatura la care se efectuează deformarea, se face distincția între prelucrarea termomecanică la temperatură înaltă (HTMT) și prelucrarea termomecanică la temperatură joasă (LTMT).
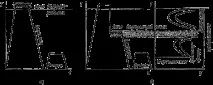
Figura 4 - Schema modurilor de joasă temperaturăprelucrarea termomecanica a otelului
Tratament termomecanic la temperatură joasă, deși oferă o întărire mai mare, nu reduce tendința oțelului de a tempera fragilitate. În plus, necesită grade mari de deformare (75...95%), deci sunt necesare echipamente puternice.
Proprietățile mecanice după diferite tipuri de TMT pentru oțeluri de inginerie au următoarele caracteristici în medie (a se vedea tabelul 1):
Tabelul 1 - Proprietățile mecanice ale oțelurilor după TMT
Desenați o diagramă de stare fier-carbură de fier, indicați componentele structurale în toate zonele diagramei, descrieți transformările și trasați curba de răcire (folosind regula fazei) pentru un aliaj care conține 1,0% C. Care este structura acestui aliaj la temperatura camerei și cum se numește acest aliaj?
Cristalizarea primară a aliajelor sistemului fier-carbon începe la atingerea temperaturilor corespunzătoare liniei ABCD (linia lichidului) și se termină la temperaturi care formează linia AHJECF (linia solidă).
La temperaturi corespunzătoare liniei BC, austenita cristalizează din soluția lichidă. În aliajele care conțin de la 4,3% până la 6,67% carbon, la temperaturi corespunzătoare liniei CD, cristalele de cementită primară încep să precipite. Cementitul care cristalizează din fază lichidă se numește primar. În punctul C la o temperatură de 1147°C și o concentrație de carbon în soluția lichidă de 4,3%, se formează un eutectic, care se numește ledeburit. Transformarea eutectică cu formarea ledeburitului poate fi scrisă ca YP4.3L[A2.14+C6.67]. Procesul de cristalizare primară a fontei se termină de-a lungul liniei ECF cu formarea ledeburitului.
Astfel, structura fontelor sub 1147°C va fi: hipoeutectic - austenit + ledeburit, eutectic -ledeburit și hipereutectic - cementit (primar) + ledeburit.
Transformările care apar în stare solidă se numesc cristalizare secundară. Ele sunt asociate cu tranziția γ-fierului la α-fier la răcire și descompunerea austenitei.
Linia GS corespunde temperaturilor de la începutul transformării austenitei în ferită. Sub linia GS, aliajele sunt compuse din ferită și austenită.
Linia E S arată temperaturile la care cementitul începe să precipite din austenită datorită scăderii solubilității carbonului în austenită odată cu scăderea temperaturii. Cementitul eliberat din austenită se numește cementită secundară.
În punctul S la o temperatură de 727 ° C și o concentrație de carbon în austenită de 0,8%, se formează un amestec eutectoid format din ferită și cementită, care se numește perlit. Perlita se obține ca urmare a precipitării simultane a particulelor de ferită și cementită din austenită. Procesul de transformare a austenitei în perlit poate fi scris ca A0.8P[F0.03+Ts6.67].
Linia PQ indică o scădere a solubilității carbonului în ferită la răcirea și precipitarea cementitei, care se numește cementită terțiară.
Prin urmare, aliajele care conțin mai puțin de 0,008% carbon (punctul Q) sunt monofazate și au o structură de ferită pură, iar aliajele care conțin carbon de la 0,008 la 0,03% au o structură terțiară ferită + cementită și se numesc fier tehnic.
Oțelurile hipoeutectoide la temperaturi sub 727ºС au structura ferită + perlită și oțeluri hipereutectoide - perlită + cementită secundară sub formă de grilă de-a lungul limitelor de granule.
În fontele hipoeutectice în intervalul de temperatură 1147–727ºС, în timpul răcirii, cementitul secundar este eliberat din austenită, datorită scăderii solubilității carbonului (linia ES). La atingerea unei temperaturi de 727ºС (linia PSK), austenita sa epuizat în carbon la0,8% (punctul S), transformându-se în perlit. Astfel, dupa racirea finala, structura fontelor hipoeutectice este formata din perlit, cementita secundara si ledeburita transformata (perlita + cementita).
Structura fontelor eutectice la temperaturi sub 727ºС constă din ledeburit transformat. Fonta hiperutectică la temperaturi sub 727ºС constă din ledeburit transformat și cementită primară.
Regula fazelor stabilește relația dintre numărul de grade de libertate, numărul de componente și numărul de faze și se exprimă prin ecuația:
unde C este numărul de grade de libertate ale sistemului;
K este numărul de componente care formează sistemul;
1 este numărul de factori externi (considerăm doar temperatura ca factor extern, deoarece presiunea, cu excepția presiunii foarte mari, are un efect redus asupra echilibrului de fază al aliajelor în stare solidă și lichidă);
Ф este numărul de faze aflate în echilibru.
Un aliaj de fier cu carbon care conține 1,0% C se numește oțel hipereutectoid. Structura sa la temperatura camerei este Cementit (secundar) + Perlit.
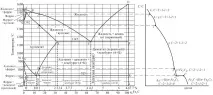
Figura 3: a - diagrama fier-cementită, b -curba de răcire pentru un aliaj care conține 1,0% carbon
Care este esența și scopul împușcării?
Creșterea durabilității pieselor mașinii prin deformarea plastică a suprafeței (SPD) sau întărirea la suprafață este utilizată pe scară largă în industrie pentru a crește rezistența la oboseala cu ciclu scăzut și ciclu înalt a pieselor mașinii.
Întărirea suprafețeiprin granulație se realizează datorită energiei cinetice a fluxului de împușcare de fier sau oțel; fluxul de împușcătură către suprafața de tratat este direcționat fie printr-un flux de aer de mare viteză, fie printr-un blaster rotativ.
Întărire - schimbarestructura și proprietățile unui material metalic cauzate de deformarea plastică. Călirea reduce ductilitatea și duritatea, dar crește limita de proporționalitate, limita de curgere și duritatea. Întărirea reduce rezistența materialului la deformarea semnului opus. Odată cu întărirea suprafeței, starea de tensiune reziduală în material se schimbă și rezistența la oboseală crește. Călirea la rece are loc în timpul prelucrării metalelor prin presiune (laminare, trefilare, forjare, ștanțare), tăiere, la rularea în role și în timpul prelucrărilor speciale cu împușcare.
Întărirea metalului în procesul de deformare plastică (călire) se explică prin creșterea numărului de defecte în structura cristalină (dislocații, vacante, atomi interstițiali). O creștere a densității defectelor în structura cristalină împiedică mișcarea noilor dislocații individuale și, în consecință, crește rezistența la deformare și reduce plasticitatea. Creșterea densității luxațiilor este de cea mai mare importanță, deoarece interacțiunea care apare între ele încetinește mișcarea lor ulterioară.
Creșterea durabilității pieselor mașinii prin deformarea plastică a suprafeței (SPD) sau întărirea la suprafață este utilizată pe scară largă în industrie pentru a crește rezistența la oboseala cu ciclu scăzut și ciclu înalt a pieselor mașinii. Figura 4 prezintă diagrame ale diferitelor PPD-uri.
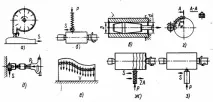
a - tratament de întărire prin shot-peening; b - finisare - alergăm într-o minge; in - prelucrare prin lustruire; d - finisare cu bila centrifuga; e - prelucrare prin urmărire; e - întărire prin explozie; g - întărire prin laminare prin vibrații; h - netezire cu diamant
Figura 2 - Scheme de deformare plastică a suprafeței
Întărirea suprafeței se realizează:
1) shot peening în spatecalculul energiei cinetice a fluxului de împușcături de fier sau oțel; fluxul de împușcare către suprafața tratată este direcționat fie printr-un flux de aer de mare viteză, fie printr-un împușcător rotativ (Fig. 2, a);
2) întărirea bile centrifugă datorită energiei cinetice a bilelor (rolelor) de oțel situate la periferia unui disc rotativ; când discul se rotește sub acțiunea forței centrifuge, bilele sunt aruncate la periferia jantei, interacționează cu suprafața tratată și sunt aruncate în adâncimea cuibului;
3) rulați cu o bilă sau o rolă de oțel (60 HRC) (Fig. 2, b); transferul de sarcină la rolă poate fi cu contact rigid și elastic între unealtă și suprafața de tratat;
4) netezire cu diamant cu un dorn cu un diamant lipit în partea de lucru (Fig. 2, h); vă permite să obțineți o suprafață lucioasă cu rugozitate scăzută.